Top CMMS Software of 2021: In-Depth Analysis
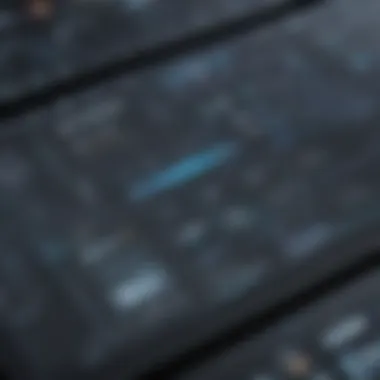
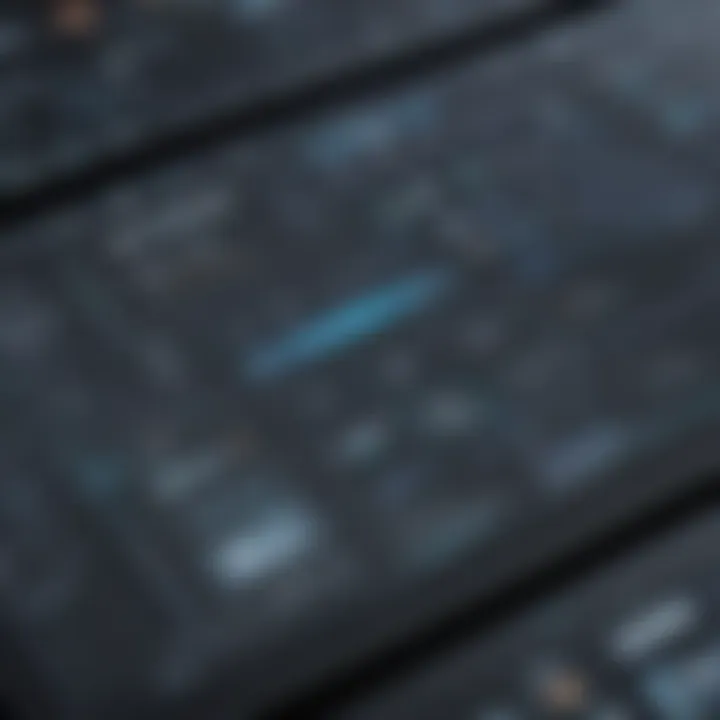
Intro
Navigating the sea of Computerized Maintenance Management Systems (CMMS) can often feel like searching for a needle in a haystack, especially for business leaders and IT professionals in the demanding pace of 2021. As maintenance management becomes a priority in optimizing operations, picking the right software can significantly make or break an enterpriseβs efficiency. With so many choices available, from cloud-based solutions to desktop applications, understanding what works best for your organization is vital.
This article aims to unpack the intricate landscape of CMMS software in 2021, focusing on the core functionalities, emerging trends, and unique attributes that different systems offer. Whether youβre part of a burgeoning small business or an established medium-sized enterprise, you will find valuable insights here tailored for your organizational needs.
The goal is not just to highlight various systems, but to equip decision-makers with the knowledge they need to assess their options effectively.
Functionality
Core Features Overview
At its heart, a CMMS is designed to make maintenance management manageable, often embodying a suite of key features that serve specific operational needs. Understanding these functionalities provides a foundation for evaluating different software platforms.
Typical core features of most CMMS include:
- Work Order Management: The ability to create, assign, and track work orders efficiently.
- Asset Management: Keeping tabs on assets, including their location, status, and maintenance history.
- Preventive Maintenance: Scheduling regular checks to avert costly breakdowns before they happen.
While these features serve as standard offerings, different products may excel in unique areas. For example, a system that integrates mobile capabilities allows technicians to access and update work orders in real-timeβcritical for minimizing downtime.
"Knowing your core needs is the first step to choosing the right software; itβs not a one-size-fits-all situation."
Unique Selling Points
Each CMMS comes with its own flavor, so to speak, setting it apart from its competitors. A strong unique selling point might be its user interface, particularly how intuitive it is for users who may not be tech-savvy. For instance, Hippo CMMS is often praised for its straightforward design and user-friendliness. Alternatively, eMaint provides extensive customization options, allowing organizations to tailor functionalities according to their specific operational requirements.
When selecting a system, a unique aspect to consider may also be the customer support provided. Some companies, like Maintenance Connection, offer robust support through various channels, ensuring that users can get help when needed.
Integrations
Compatible Tools
In an increasingly interconnected world, the ability to integrate with other software tools is becoming a game changer for CMMS platforms. A great CMMS allows smooth data sharing with existing systems, such as accounting software, ERP systems, or even IoT devices for real-time data analytics. This compatibility not only streamlines maintenance processes but also enhances overall operational efficiency.
For instance, Fiix stands out due to its ability to integrate seamlessly with various applications like QuickBooks and Zapier, allowing for a more cohesive operational setup.
API Availability
An often overlooked factor in the selection process is the availability of API (Application Programming Interface). It allows businesses to customize their software experiences and boost interconnectivity between CMMS and other essential tools. Software like UpKeep offers well-documented APIs, empowering tech teams to build bespoke integrations that can serve specific business functions, ultimately modifying how information flows within an organization.
Understanding CMMS Software
In the realm of modern business operations, understanding CMMS software is crucial, particularly for small to medium-sized businesses striving to enhance their maintenance management processes. Computerized Maintenance Management Systems are designed to streamline maintenance activities, leading to increased productivity and efficiency. This section uncovers the essential aspects of CMMS, offering insights that are not only theoretical but also practical for decision-makers.
Definition and Purpose
At its core, CMMS software acts as a centralized platform that helps organizations manage their maintenance tasks and activities. It plays a pivotal role in tracking and scheduling maintenance work, ensuring that equipment and assets are maintained properly to prevent costly breakdowns and downtime. By utilizing this technology, businesses can achieve a deeper understanding of their operational needs and enhance their maintenance strategies.
The primary purposes of CMMS software include:
- Preventive Maintenance: Planning and executing maintenance tasks to reduce the risk of unexpected failures.
- Work Order Management: Streamlining the creation, assignment, and tracking of maintenance tasks.
- Data Management: Centralizing information related to assets, inventory, and maintenance history.
Key Components of CMMS
For those looking to dive deeper into the capabilities of CMMS, it's important to know the key components that make these systems valuable.
Work Order Management
Work Order Management is a critical feature of any CMMS. It allows businesses to create and manage work orders efficiently, which is essential for keeping maintenance workflows smooth. This includes assigning tasks, tracking completion, and monitoring labor and materials used in each work order. One prominent characteristic of Work Order Management is its ability to automate scheduling. This helps ensure that tasks are not forgotten and resources are allocated effectively.
An unsung benefit of Work Order Management is its reporting capabilities. By generating detailed reports, companies can analyze labor productivity and equipment performance, providing insight into operational efficiency.
Asset Tracking
Asset Tracking is another cornerstone of CMMS software. This component enables businesses to maintain an accurate inventory of their assets. Knowing the status, location, and history of assets can significantly impact maintenance strategies and decision-making processes. One particularly rewarding feature of Asset Tracking is real-time monitoring, which can alert managers about potential issues before they escalate.
The unique advantage of Asset Tracking within a CMMS is that it fosters better resource planning and reduces the chances of asset-related downtime. However, it does require a disciplined approach to data entry and management, as accuracy is key here.
Inventory Management
Inventory Management in CMMS focuses on controlling spare parts and supplies essential for maintenance work. It allows organizations to monitor stock levels, reorder supplies, and track inventory used in maintenance tasks. A key characteristic of this component is its integration with other features, such as Work Order Management, to ensure that the necessary parts are available when needed.
As opposed to traditional inventory systems, CMMS inventory management not only helps avoid stockouts but also minimizes excess inventory holding costs. Nevertheless, it demands a commitment to regular audits and updates to maintain accurate data.
"The adoption of CMMS not only simplifies processes but also empowers businesses to make informed decisions through data analysis."
In summary, understanding the intricacies of CMMS software, from its definition to its components, equips decision-makers with the knowledge to leverage this technology effectively. By focusing on elements like Work Order Management, Asset Tracking, and Inventory Management, organizations can ensure a more streamlined maintenance process.
The Evolution of CMMS Software
The realm of Computerized Maintenance Management Systems (CMMS) is as dynamic as the industries it serves. Understanding how CMMS software has evolved is key for decision-makers, especially in small to medium-sized businesses. As technology progresses, these systems have transformed significantly to meet the needs of modern operations. This evolution tells a compelling story of innovation, adaptability, and increasing dependence on data-driven decision-making. In this context, recognizing the historical journeys of CMMS can guide organizations in choosing the right tools for their maintenance needs.
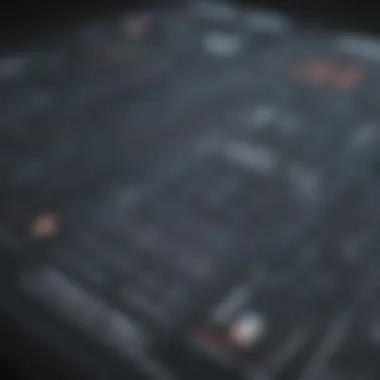
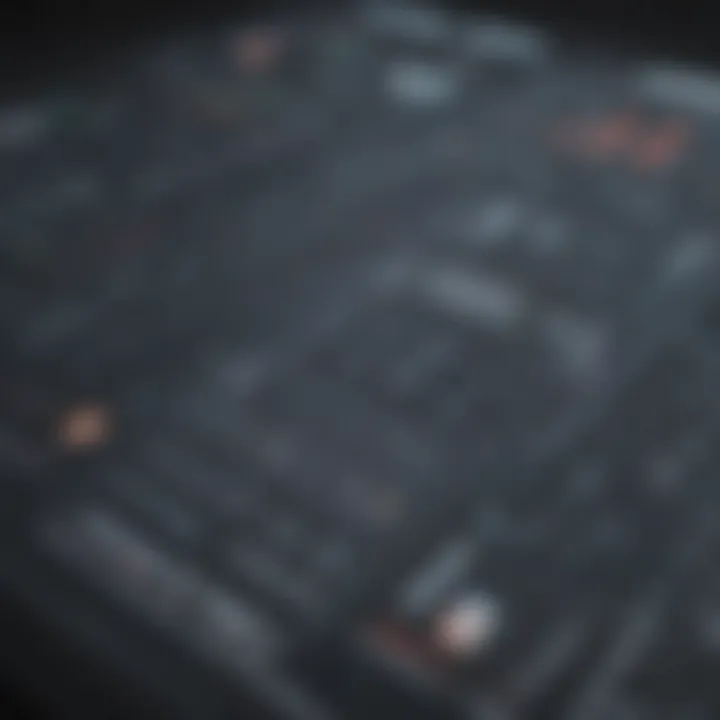
Historical Context
CMMS software has roots that stretch back to the late 20th century. Originally, maintenance management was a paper-based process, often reliant on manual logs and extensive spreadsheets. Organizations struggled to maintain accuracy, leading to inefficiencies and increased operational costs. The first iterations of CMMS emerged as simple databases, designed to transition companies from paper to digital.
By the mid-1980s, businesses began to realize the potential of computerized systems in streamlining maintenance processes. Investments in data management paved the way for the development of specialized software. These systems primarily focused on basic functionalities such as tracking work orders and managing asset schedules, enhancing overall operation management.
Whatβs noteworthy is that during this early phase, CMMS was often viewed as an additional cost rather than a crucial asset. However, organizations gradually recognized the benefits of real-time tracking and reporting capabilities. This pivotal moment ignited a shift in how maintenance was perceived within the business hierarchy, elevating its status from mere operational necessity to a strategic component of organizational success.
Recent Developments
Fast forward to the present, the CMMS landscape is vastly different. Recent developments can be attributed to advances in technology and changing business needs. One of the most notable trends includes cloud-based solutions. These systems allow for remote access, ensuring that teams can monitor and manage maintenance processes from anywhere in the world. This shift not only boosts flexibility but also reduces the overhead costs associated with on-premise solutions.
Another significant advancement is the integration of IoT (Internet of Things). Sensors embedded in equipment are now capable of feeding real-time data into CMMS, alerting maintenance teams when an asset requires service. This predictive maintenance approach can be a game-changer, minimizing downtime and optimizing resource allocation. Such integration can also lead to better asset longevity and reduced overall maintenance costs.
Additionally, the rise of mobile applications has transformed user interaction with CMMS. Maintenance professionals can access work orders, update status, and even capture data right from their smartphones or tablets. This shift to mobile not only improves responsiveness but also fosters a culture of proactive maintenance and accountability.
"Understanding the evolution of CMMS helps businesses align their operational strategies with modern technological advances, ensuring they remain competitive in their respective industries."
To wrap it up, the evolution of CMMS software from rudimentary systems to sophisticated, integrated solutions illustrates the technologyβs adaptability to industry demands. This development not only enhances maintenance management processes but also offers significant insights into how organizations can effectively use these tools to their advantage. As we continue our exploration into CMMS, the importance of these advancements will remain at the forefront of achieving operational excellence.
Criteria for Evaluating CMMS Solutions
Choosing the right CMMS software can feel like searching for a needle in a haystack. With so many options on the table, itβs essential to know what to look for when evaluating these systems. The criteria outlined here will help demystify the selection process, highlighting the essential elements, benefits, and considerations to keep in mind.
User Interface and Experience
User interface (UI) and user experience (UX) play critical roles in a CMMS software's effectiveness. You want a system that is intuitive and user-friendly, or else you risk frustrating your team rather than empowering them. A well-designed UI ensures that users can quickly navigate the software, reducing the time it takes to learn the system. Think of it as the cake and icing; while the cake is the underlying functionality, the icing makes it appealing and enjoyable to use.
Key aspects to consider in UI/UX include:
- Navigation Ease: Is it simple to find what you need without wandering around?
- Visual Design: Does the interface look modern and organized, helping users feel at ease?
- Customization Options: Can users tailor the dashboard and layout to better fit their unique tasks?
When teams find the software easy to use, theyβre likely to adopt it faster, leading to increased productivity.
Integration Capabilities
Integration capabilities are crucial because businesses today often rely on various software solutions to handle different tasks. A CMMS that can seamlessly connect with existing systemsβlike ERP, inventory management, or human resourcesβcan boost data accuracy and streamline operations.
Things to consider in integration include:
- API Availability: Does the CMMS provide a public API that eases communication with other systems?
- Pre-Built Connectors: Are there existing integrations that you can easily set up without custom development?
- Data Synchronization: How well does the software maintain data consistency across platforms?
Effective integration helps eliminate siloed data, making your organization more agile and adaptive to changes in demand or workflow.
Scalability Considerations
As businesses grow, their needs change. A CMMS solution must be able to grow alongside your organization without requiring a complete overhaul. Scalability involves both the ability to scale the software's features and functionality, as well as its capacity to handle an increasing amount of data and users.
Here are some factors to ponder:
- User Limits: What is the maximum number of users before performance starts to decline?
- Feature Expansion: Can you easily add advanced features as your operations evolve?
- Performance Metrics: How well does the system perform under increased loads?
Selecting a scalable system helps future-proof your investment, ensuring you donβt have to switch to a different provider as your needs grow.
Cost and Licensing Models
When discussing CMMS solutions, cost is always a key player. However, itβs not just about the price tag; various licensing models exist, and understanding these can help you make a more educated decision.
Evaluating cost factors involves:
- Upfront Fees vs. Subscription: Are you looking at one-time purchases, or will you be paying ongoing subscription fees? Each has its pros and cons.
- Hidden Costs: Check for add-on charges that might pop up down the line, such as training or support.
- Return on Investment: How quickly can you expect return on your investment through improved efficiency and reduced downtime?
It's important to weigh the total cost of ownership against the anticipated benefits to ensure you aren't just chasing the cheapest option.
"Selecting CMMS software isn't just a purchase; it's a long-term partnership. Investing wisely can lead to significant operational improvements."
By meticulously weighing these criteria, you're not merely choosing software; you're laying down the foundation for efficient maintenance management suitable for your organizationβs unique needs.
Top CMMS Solutions of
Selecting the right CMMS solution is a pivotal moment for any organization looking to streamline its maintenance processes. In 2021, the market saw a competitive array of software tailored to meet various needs. Understanding the standout options provides businesses with valuable insights into functionalities, user experiences, and industry applications. This section highlights the features, pros and cons, and industry use cases of some of the leading CMMS solutions, guiding decision-makers towards informed choices.
CMMS Solution A
Features Overview
CMMS Solution A is designed with an intuitive interface that makes navigation a breeze even for those new to the software. One notable characteristic of Solution A is its comprehensive work order tracking feature. Users can create, assign, and monitor work orders efficiently, which streamlines maintenance activities.
A unique advantage of this solution lies in its real-time dashboards. Users can access key metrics at a glance, helping them make informed decisions swiftly. Despite its benefits, some users have noted that the extensive features may overwhelm those who only need basic functionality.
Pros and Cons
When weighing the pros and cons of CMMS Solution A, the standout aspect is its robust reporting capabilities. This feature allows businesses to analyze maintenance trends over time, enhancing decision-making and forecasting functionalities. However, a drawback is the softwareβs pricing, which may be considered steep for small businesses.
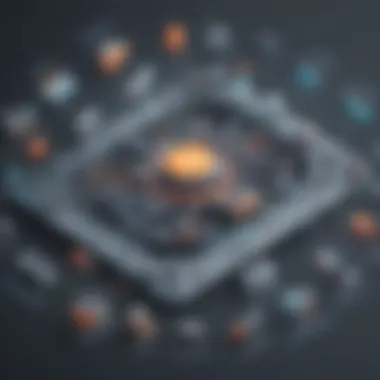
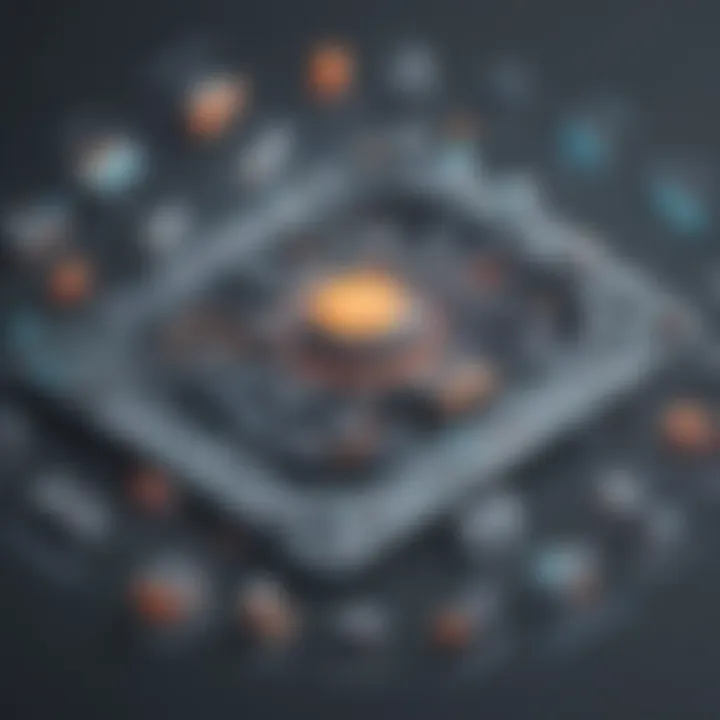
Another unique point is its strong customer support, which provides tiered assistance based on user subscription levels, but this can lead to frustration for users eager for immediate help at no additional cost.
Industry Applications
CMMS Solution A shines in the manufacturing and healthcare sectors. Its capabilities for tracking equipment maintenance and regulatory compliance make it a favored choice among these industries. The unique benefit of this application is that it aids in minimizing downtime, which is critical in high-stakes environments. Yet, some users from less intensive sectors have reported that the high level of features may not be necessary, leading to inefficiencies for simpler maintenance tasks.
CMMS Solution B
Features Overview
Turning to CMMS Solution B, one of its key characteristics is its mobile accessibility. This feature allows maintenance teams to receive updates and manage work orders directly from their smartphones, facilitating operations on the go. The added benefit is that it keeps teams connected, even when they are out in the field.
However, some users have mentioned that the mobile app's user experience doesnβt always match that of the desktop version, resulting in occasional frustrations.
Pros and Cons
The user-friendliness of CMMS Solution B is a significant advantage; it has earned praise for simplifying complex processes typically associated with maintenance management. Nevertheless, potential cons include limited customization options, which could deter organizations looking for tailored solutions.
Furthermore, the pricing model is subscription-based, leading to concerns among some businesses about long-term costs. The ease of updates can also be seen as a double-edged sword; while users get new features regularly, constant changes can sometimes lead to confusion about how to navigate updates.
Industry Applications
CMMS Solution B has found traction mainly in the retail and hospitality sectors. Its features align well with the fast-paced, high-demand environments where efficiency is crucial. One particular advantage is that it supports inventory management, ensuring the right supplies are available for maintenance tasks. On the downside, smaller firms have expressed that the software may have features they donβt require, translating to excess costs without proportional benefit.
CMMS Solution
Features Overview
Lastly, CMMS Solution C distinguishes itself through its integration capabilities with various other platforms such as ERP systems. This seamless integration is a key selling point as it allows for a smoother flow of information across departments, minimizing data entry errors.
A unique feature in Solution C is its predictive maintenance capability based on historical data analysis, which aids companies in preventing equipment failures before they happen. However, it can require an investment in training to maximize this feature effectively.
Pros and Cons
The major advantage of CMMS Solution C is its adaptability across various sectors, which is beneficial for organizations with diverse operational needs. Yet, its complexity might be a point of contention for enterprises looking for quick fixes without diving into detailed analytics.
The softwareβs licensing structure has been flagged as complex, which may deter potential users; many appreciate clear cost breakdowns. The ongoing updates and upgrades can also create patchwork connectivity between the platform and older systems within businesses.
Industry Applications
CMMS Solution C is well-suited for industries like utilities and construction, where the ability to predict and prevent issues can save both time and money. Its unique feature of drill-down analysis allows businesses to assess specific equipment lifecycle performance, which is invaluable in asset-heavy sectors. On the downside, businesses that require quick, simple solutions might find this software cumbersome and overly complex for their maintenance needs.
Benefits of Implementing CMMS Software
Adopting a Computerized Maintenance Management System (CMMS) can significantly boost the efficiency of maintenance operations, particularly for small to medium-sized businesses. As these enterprises often juggle limited resources while trying to keep up with their maintenance tasks, the ability to streamline processes becomes paramount. CMMS software offers a variety of benefits that can not only enhance operations but also contribute to a more organized and manageable approach to facility maintenance.
Increased Efficiency
When it comes to maintenance work, efficiency is king. A well-implemented CMMS enables technicians to prioritize tasks, track work orders, and manage resources more effectively. Rather than relying on spreadsheets or paper lists, a CMMS provides a centralized platform to view all activities. This not only cuts down on time spent searching for information but also ensures that no tasks slip through the cracks.
Think about it: if a technician is dispatched to fix a machine but has no context about past repairs, crucial information might be overlooked. A CMMS allows maintenance teams to retrieve historical data quickly, identifying what parts might be needed or what issues are recurring. This leads to more informed repairs and less downtime.
Here are a few key points on how CMMS software can drive efficiency:
- Work Order Automation: Automatic reminders and work order assignments prevent bottlenecks.
- Resource Allocation: Track availability and assign the right people to the right tasks, saving time and improving morale.
- Streamlined Communication: Share updates instantly with team members, ensuring everyone is in the loop.
Enhanced Data Management
Data is the lifeblood of any operation, and with CMMS software, managing that data becomes streamlined and intuitive. With the ability to gather, analyze, and report on various maintenance metrics, businesses can gain insights that were previously hard to come by. This dramatic shift in data handling can lead to smarter decision-making.
For instance, detailed reporting functionalities allow organizations to foresee maintenance needs before they escalate. Analyze trends in equipment performance or track maintenance costs over time. This data-driven approach not only optimizes resources but also aids strategic planning.
In terms of data management, consider the following aspects:
- Centralized Information Storage: All key maintenance data in one place, minimizing confusion.
- Historical Data Records: Keep detailed records of past maintenance activities for future reference.
- Customizable Dashboards: Focus on the metrics that matter most to your business priorities.
Improved Compliance and Reporting
In industries with stringent regulatory requirements, compliance is non-negotiable. CMMS software helps ensure that maintenance schedules are adhered to, which is critical in avoiding legal pitfalls. By maintaining detailed records and generating automated reports, businesses can easily showcase their adherence to regulations, making audits much simpler.
Additionally, CMMS provides capabilities that help organizations align with industry standards. Whether itβs keeping track of inspections or managing safety protocols, having this information readily available not only supports compliance but also enhances overall safety in the workplace.
Key elements of compliance and reporting enhancements include:
- Automated Compliance Alerts: Alerts for upcoming maintenance due dates or regulatory checks.
- Easily Accessible Reporting Tools: Generate reports tailored to internal and external requirements.
- Risk Management Features: Improved tracking of equipment conditions and failure rates to mitigate risks.
"Investing in CMMS software not only simplifies maintenance tasks but can also lead to discovering hidden assets, managing expenses, and ultimately maximizing productivity."
As businesses increasingly recognize the advantages of CMMS software, it becomes clear that these systems are not merely tools for task management, but vital allies in strategic maintenance management. The ability to enhance efficiency, streamline data, and improve compliance creates an environment where maintenance can thrive and contribute significantly to a companyβs bottom line.
Challenges to Consider When Choosing CMMS Software
When evaluating CMMS software, decision-makers often face several challenges that can impact their ability to effectively implement and utilize these systems within their organizations. Recognizing these challenges is crucial, as it aids in making a well-informed decision that aligns with the objectives of the business. This section delves into the hurdles that can arise, particularly focusing on implementation barriers and training requirements.
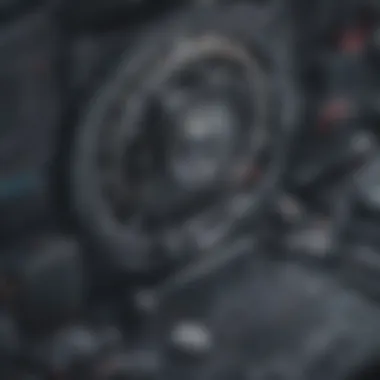
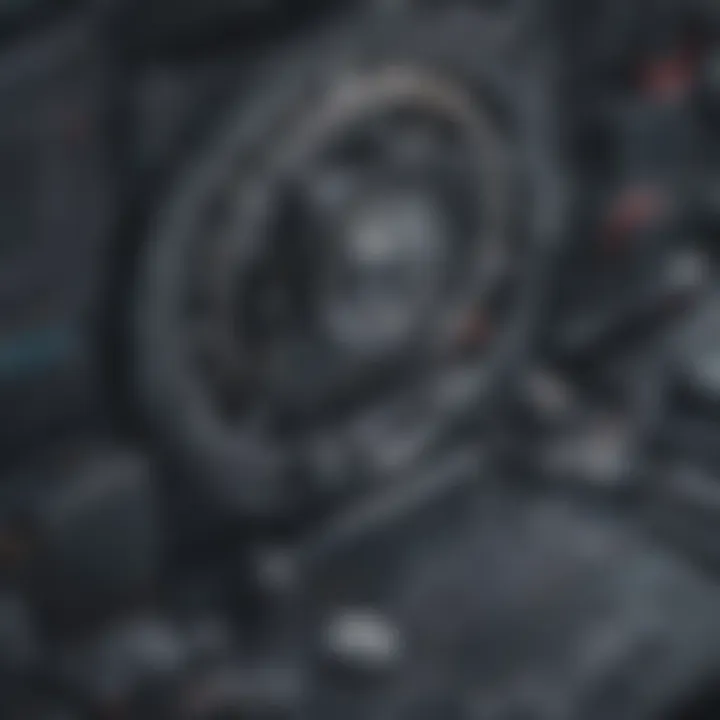
Implementation Barriers
Implementing a new CMMS can feel a bit like trying to fit a square peg into a round hole. Businesses often underestimate the complexity involved in transitioning from their existing systems to a CMMS framework. First off, data migration is a significant hurdle. Moving historical maintenance data to the new system requires careful planning, especially to avoid data loss or corruption. If the data isnβt cleaned and organized before migration, it can create chaos down the line.
Additionally, integration with other software systems can be tricky. Many small to medium-sized businesses use various tools for inventory management, finance, and more. Ensuring that the new CMMS communicates effectively with these existing systems may require additional resources and technical know-how.
Furthermore, varying levels of resistance from staff can slow down the implementation process. Employees may be comfortable with their current processes and wary of change. This reluctance could lead to lower engagement with the new system, limiting its effectiveness. Addressing these concerns early on is essential.
"A project manager's greatest asset often isn't the software itself, but the trust and enthusiasm of the team working with it."
Therefore, evaluating potential barriers like data migration, integration issues, and staff resistance is imperative before selecting a CMMS solution.
Training Requirements
Once a CMMS has been chosen, the next challenge often revolves around training staff to use it effectively. Many CMMS providers include training as part of their offering, but the depth and format of this training can vary widely.
Small to medium-sized businesses often face resource constraints. Allocating time for training can feel like pushing a boulder uphill when there are day-to-day operations to manage. This is where many companies find themselves struggling. If workers donβt receive adequate training, they might default to their old manual methods out of frustration. Itβs important to provide clear training sessions that are neither too bland nor too overwhelming.
Moreover, the learning curve associated with new technologies can vary. While younger employees might adapt quickly, seasoned staff might need through, practical training.
To facilitate effective training, consider the following strategies:
- Customization: Tailor the training to meet specific departmental needs, making it relevant and engaging.
- Ongoing Support: Offering ongoing support can help maintain momentum, especially during the early weeks post-implementation.
- Feedback Loops: Establishing avenues for feedback allows employees to voice challenges or questions.
In sum, understanding the implementation barriers and the necessary training requirements will prepare businesses for the complex path toward adopting CMMS software. By addressing these elements up front, organizations can pave the way for a smoother transition and ongoing operational efficiency.
Future Trends in CMMS Software
The realm of Computerized Maintenance Management Systems is constantly evolving, driven by advancements in technology and changing business needs. Staying abreast of future trends in CMMS software is crucial for businesses aiming to enhance maintenance management processes. Recognizing these trends not only arms organizations with the tools for better efficiency but also positions them as frontrunners in their respective sectors. In this section, we will explore three significant aspects shaping the future of CMMS software: automation and AI integration, mobile accessibility, and sustainability considerations.
Automation and AI Integration
With the rise of automation, CMMS software has been gearing up to leave behind the manual processes that slow down productivity. Integrating artificial intelligence can lead to smarter work order management, predictive maintenance, and more streamlined inventory control.
Imagine a scenario where equipment data feeds into the CMMS in real-time, allowing the software to predict failures before they occur. Such foresight can mitigate downtime significantly, saving businesses not just time but also hefty repair costs. In fact, companies that adopt AI-driven CMMS tools often notice a notable increase in asset lifespan and operational efficiency.
- Benefits of automation in CMMS:
- Reduction in manual labor
- Enhanced accuracy in data tracking
- Predictive analytics for maintenance
As organizations become more familiar with AI functionalities, there's an apparent shift toward using such solutions to inform decision-making. The interface between technology and human expertise will likely represent a new wave of operational efficiencies across industries.
Mobile Accessibility
In a world where we carry powerful computing devices in our pockets, CMMS providers have recognized the critical need for mobile accessibility. Mobile-friendly platforms allow maintenance teams to access crucial information on-the-go, whether they are in the field or on the shop floor.
This shift is not about just having a mobile app; itβs about utility and functionality. Users can input data, retrieve work orders, and manage inventories directly from their devices without the need to be tethered to their desks.
- Key advantages of mobile CMMS:
- Instant updates mean real-time data integrity
- Enhanced communication pathways among teams
- Timely responses to issues as they arise
According to industry reports, businesses that harness mobile accessibility within their CMMS solutions often see an increase in worker productivity. This is because personnel can act faster, thus reducing response times to issues that may arise unexpectedly.
Sustainability and Environmental Considerations
With the global focus shifting toward sustainability, CMMS software is adapting by introducing features that help organizations minimize their environmental footprint. This change reflects a growing recognition that maintenance practices can directly impact environmental sustainability.
More software solutions now include modules for tracking energy use, waste management, and maintaining eco-friendly equipment. By integrating sustainability within maintenance management pursuits, organizations can not only comply with regulations but also appeal to environmentally-conscious consumers.
- Considerations for sustainability in CMMS:
- Tracking energy consumption of assets
- Implementing equipment for greener operations
- Reporting on compliance and environmental impact
Focusing on sustainability can also lead to cost savings, as efficient resources usage often translates into reduced operational expenditures. Furthermore, in a competitive marketplace, demonstrating commitment to sustainability can differentiate a brand and strengthen customer loyalty.
"A forward-looking CMMS platform not just enhances operational efficiency; it also aligns with the broader goals of sustainability and corporate responsibility."
As we move forward, embracing these trends in CMMS software will not only pave the path for improved maintenance processes but will also contribute to long-term benefits for businesses in an increasingly aware market.
Culmination
As we draw the curtains on our exploration of CMMS software, it's crucial to grasp the underlying implications of our findings. The considerations surrounding the selection of the right computerized maintenance management system are substantial, especially in today's competitive landscape. The right CMMS can be a game changer, not just in terms of operational efficiency but also for strategic decision-making at higher management levels.
Making an Informed Choice
When contemplating a CMMS, the nuances of your specific business environment can't be overstated. An informed choice hinges on not just the features or pricing but also on how well the software aligns with your team's needs and organizational goals. Consider the following:
- Assess Your Requirements: What are the core issues you aim to resolve with a CMMS? Is it better inventory management or improved asset tracking? Pinpointing your primary needs streamlines the decision-making process.
- Evaluate Your Budget: Money talks. Ensure the potential return on investment justifies the costs involved. Remember, the cheapest option may not always be the best for your unique situation.
- Involve Stakeholders: Don't fly solo on this. Engage your team to get diverse perspectives. This collective input ensures the solution caters to actual user needs, facilitating smoother adoption.
- Explore Scalability: Look to the future. Opt for systems that can grow with your business. Whether you're aiming for international expansion or considering diversifying your service offerings, scalability should be at the forefront of your selection process.
Looking closely at these facets will enable you to navigate the choices ahead without feeling overwhelmed.
Final Recommendations
To sum things up, the pursuit for a suitable CMMS software must involve solid groundwork and thoughtful analysis. Here are some final recommendations based on our comprehensive investigation:
- Prioritize Usability: Choose a platform with an intuitive interface. If your team struggles with navigation, productivity takes a hit.
- Integration is Key: Ensure the CMMS software integrates well with existing tools and systems. This connectivity enhances efficiency and minimizes data entry errors.
- Stay Current with Trends: Trends like AI and mobile access arenβt just buzzwords; they represent the future landscape. Choose a solution that embraces these elements for long-term viability.
- Don't Skimp on Training: Implementing a new system requires proper training sessions. A well-trained team maximizes the benefits of the new software, driving productivity.
- Think Long-Term: Consider the future when choosing CMMS software. How will this choice affect your operations in the coming years? Opt for solutions that not only meet immediate needs but also align with your long-term strategic vision.
In a nutshell, the process of selecting a CMMS software may seem daunting, but armed with the right insights and strategies, you can make an informed decision that will greatly enhance your maintenance management capabilities.