The Connection Between MRP and PLM in Business
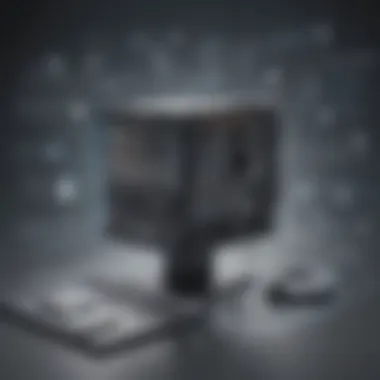
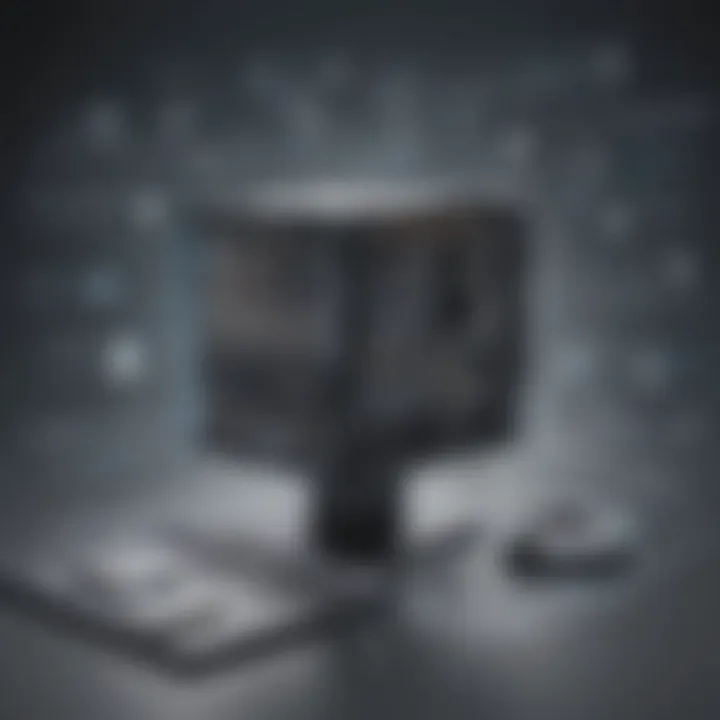
Intro
In the fast-paced world of business, where the competition is fierce, understanding the intricate relationship between Material Requirements Planning (MRP) and Product Lifecycle Management (PLM) has become vital. Businesses, especially small to medium-sized enterprises, are often caught in the webs of complexity when it comes to managing their resources and products. The integration of MRP and PLM systems can illuminate the path towards improved operational efficiency and agile decision-making.
This article seeks to dissect the collaboration between these two systems. With a finger on the pulse of contemporary practices, we will explore how MRP, primarily concerned with inventory control and scheduling, aligns with PLM to facilitate product development from inception to discontinuation. This understanding is not just for enthusiasts in supply chain management; it serves as a beacon for entrepreneurs and IT professionals who aim to implement strategies that help their organizations thrive amidst challenges.
"The bridge between MRP and PLM is not merely a connection; it is a critical pathway for innovation and productivity."
As we navigate through the functionalities of these systems, their unique selling points, and the integrations available that enhance their effectiveness, our goal is to offer a roadmap that organizations can use to streamline their processes and ultimately better serve their customers.
Prologue to MRP and PLM
In the landscape of modern business, understanding the interplay between Material Requirements Planning (MRP) and Product Lifecycle Management (PLM) emerges as not just beneficial but essential. Both systems serve as the backbone for efficient operations, driving cost-effective strategies and innovative solutions. Recognizing their distinct yet intertwined functionalities allows companies to optimize processes, enhance collaboration, and streamline decision-making. The virtues of successfully implementing MRP and PLM can be immense, particularly for small to medium-sized businesses, entrepreneurs, and IT professionals.
Defining MRP Concepts
Material Requirements Planning, or MRP, is a system that essentially revolutionizes inventory management and production scheduling. Think of it as the engine that keeps the wheels of manufacturing turning smoothly. In simple terms, MRP utilizes data from sales forecasts, customer orders, and inventory levels to schedule production and purchase necessary materials. This process can significantly improve operational efficiency by ensuring that raw materials are available for production just when theyβre needed rather than building up unnecessary stock.
When exploring MRP, it's crucial to acknowledge its key components:
- Bill of Materials (BOM): This outlines the hierarchy of materials required to produce a finished product, paving the way for precise inventory needs.
- Master Production Schedule (MPS): A detailed timeline that specifies what is to be produced, when, and in what quantities.
- Inventory Status Records: Tracking quantities on hand, committed, and available inventory to inform purchase decisions and production scheduling.
Mastering these elements allows organizations to minimize waste, reduce lead times, and improve service levels. The seamless integration of MRP into daily operations can lead to a significant boost in productivity and responsiveness to market changes.
Defining PLM Concepts
On the other side of the spectrum lies Product Lifecycle Management, often abbreviated as PLM. This system plays a vital role in managing a productβs complete lifecycleβfrom conception, design, manufacturing, to service and disposal. It encourages collaboration across various departments, ensuring that everyone is on the same page, thus minimizing miscommunication and errors.
The essence of PLM relies on centralizing information related to the product lifecycle, which has numerous advantages:
- Cross-Functional Collaboration: Teams from engineering, marketing, and quality assurance can work together, ensuring products align with business goals and customer needs.
- Data Management and Compliance: Organizations can efficiently manage regulatory requirements and standards across multiple product lines.
- Faster Time to Market: With effective PLM in place, businesses can reduce the time it takes to launch new products by streamlining processes.
Effectively implementing PLM enables enterprises to ensure product quality and innovation while enhancing overall customer satisfaction. In a world where adaptability is key, embracing PLM is more than a strategic move; itβs a necessity for staying ahead in the competitive landscape.
"In the dance of modern enterprises, MRP and PLM are two key partners that must sync to create a harmonious flow of operations."
Through understanding these foundational concepts, enterprises can navigate the complexities of integrating MRP and PLM, ultimately leading to sustainable growth and enhanced operational performance.
Historical Context of MRP and PLM
Understanding the historical context of Material Requirements Planning (MRP) and Product Lifecycle Management (PLM) is fundamental for comprehending how these systems have evolved and how they function today. The evolution of both MRP and PLM has not only shaped manufacturing and product development but has also influenced organizational structures and practices across industries. By grasping these historical roots, small to medium-sized businesses, entrepreneurs, and IT professionals can better appreciate the significance of integrating these systems into their operations.
In the early 1960s, MRP emerged as a response to growing inventory costs and inefficient production processes. Companies were facing increasing complexities in managing materials and components necessary for production. Traditional inventory management prior to MRP often relied on guesswork, leading to either excess stock or shortages. Enter MRP, with its focus on inventory management through systematic planning based on demand forecasts. It allowed companies to see smoother production lines and less wastage.
On the other hand, PLM started gaining traction in the late 1980s as companies began to recognize the necessity of managing a product's entire lifecycleβfrom concept to end-of-life. At its core, PLM seeks to centralize and streamline all information relevant to product development. This meant that organizations could innovate faster while also ensuring compliance and quality across various stages of product development.
"The history of MRP and PLM highlights how businesses adapted to challenges by leveraging technology, leading to better collaboration and efficiency."
Both MRP and PLM systems have been interwoven into the fabric of modern enterprises, as they address fundamental challenges that arose with industrial pressures and consumer demands. They complement each other far beyond just material management and product lifecycles; together, they represent a shift towards more integrated and agile business environments.
Evolution of MRP Systems
The evolution of MRP systems tracks closely with technological advancements and the ever-increasing demands for efficiency in production processes. In the 1970s, as computers became more commonplace, MRP systems began to leverage this technology, moving from manual calculations to sophisticated software tools that could handle large volumes of data. This transition marked a transformative phase that allowed businesses to optimize their inventory, schedule production more effectively, and respond quickly to changes in consumer demand.
MRP II later emerged in the 1980s, integrating financial planning and other manufacturing aspects, demonstrating how far MRP had come from its humble beginnings. The modern iterations of MRP today, often referred to as Enterprise Resource Planning (ERP) systems, incorporate a more extensive range of functionalities. This evolution reflects the need for organizations to have a holistic view of their operations, fostering better decision-making and adaptability.
Development of PLM Systems
The development of PLM systems is closely tied to the need for innovation and quality management in product development. In the late 1980s and 1990s, as businesses became more global, the complexity of managing product information increased. Various stakeholders, engineers, and even external partners needed access to a shared pool of data. This marked the beginning of PLM systems as we understand them today.
Todayβs PLM solutions offer collaboration across departments, facilitating communication between design, manufacturing, supply chain, and marketing teams. As a result, organizations can streamline product launches and enhance overall product quality. Furthermore, with the advancements in technologies such as cloud computing and big data analytics, PLM systems can now support real-time information sharing and enhance data-driven decision-making processes.
The historical context highlights how both MRP and PLM have dynamically evolved in response to challenges that manufacturing and product development face, paving the way for future improvements and integration strategies. Organizations that take the time to reflect on this development are better equipped to harness these systems effectively, thereby maximizing their operational efficiency.
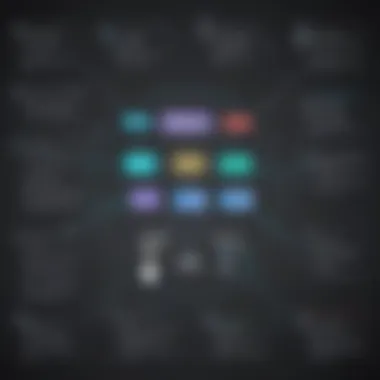
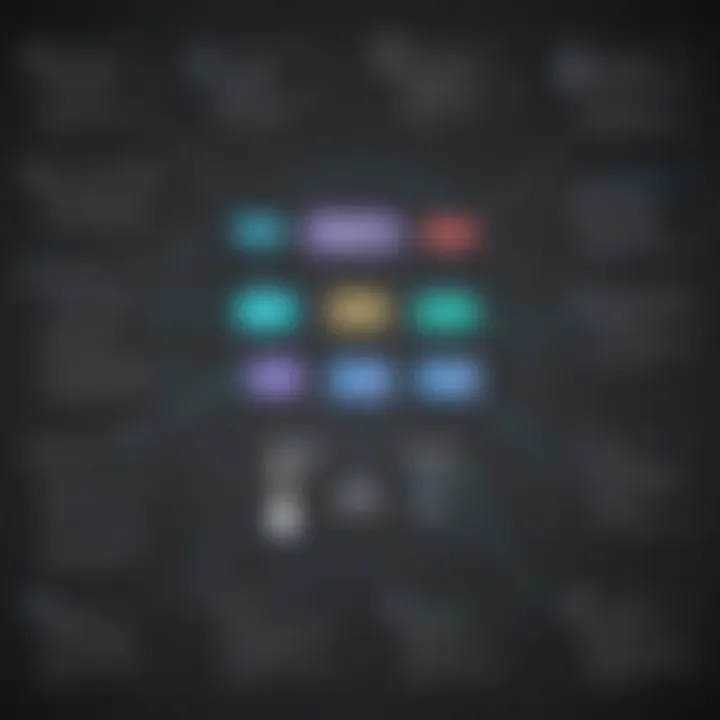
Core Principles of MRP
Material Requirements Planning, or MRP for short, is far from just a set of guidelines for managing inventory. It's a strategic tool that enables businesses to ensure that they have the right materials, at the right time, and in the right quantities to meet production demands. The relevance of MRP principles in modern enterprises cannot be overstated. An efficient MRP system can drastically impact an organization's operational effectiveness, productivity, and overall profitability. Understanding MRP principles is crucial for managing supply chains, especially in small to medium-sized companies that may not have extensive resources like larger corporations.
Inventory Management Techniques
Effective inventory management is a linchpin in MRP systems. The primary goal is to maintain inventory levels that are neither too high nor too low. Striking this balance reduces holding costs while also ensuring that materials are available to meet production schedules. There are several key techniques for effective inventory management:
- Just-In-Time (JIT): This technique emphasizes reducing inventory levels by ensuring materials arrive just as they are needed in the production process. For many businesses, the challenge is to build strong relationships with suppliers to ensure reliability.
- ABC Analysis: This method categorizes inventory into three groups based on importance. "A" items are high-value products with low frequency of sales, "B" items are moderate value and moderate frequency, and "C" items are low-value with high frequency. Understanding these categories helps focus on where to allocate resources most effectively.
- Safety Stock: Maintaining a buffer stock is wiseβit's all about managing uncertainties in supply and demand. Calculating safety stock levels can help organizations avoid stockouts that could halt production.
These techniques can each contribute to a more streamlined supply chain and ensure that businesses are ready to meet their production commitments without unnecessary waste.
Demand Forecasting Methods
Another core principle of MRP is demand forecasting, which involves making educated estimates about future customer demand. Accurate demand forecasting is fundamental for ensuring that inventory levels are optimal. Some common methods for demand forecasting include:
- Quantitative Methods: These rely on historical sales data to predict future trends. Techniques can include time series analysis or causal models. For instance, a company could analyze past sales during holiday seasons to anticipate future demand spikes.
- Qualitative Methods: When past data may not adequately reflect future trendsβlike in the case of new product launchesβqualitative forecasting techniques become essential. Engaging with sales teams or conducting market research can yield insights that pure data might not reveal.
- Collaborative Forecasting: Involving cross-departmental input can enhance forecasting accuracy. When sales, marketing, and production teams share insights, the predictions are often more grounded in organizational realities.
To excel in MRP, itβs vital to recognize that both inventory management techniques and demand forecasting methods work hand-in-hand. Leaning heavily on one without regard for the other can lead to systemic failures, such as overproduction or stockouts.
Core Principles of PLM
When we talk about Product Lifecycle Management (PLM), itβs akin to understanding the very backbone of product management in organizations. The principles that govern PLM can make or break how effectively a company can navigate its productβs journey from inception through to retirement. Emphasizing these core principles not only streamlines processes but also ensures that the organization can adapt quickly to market dynamics and customer needs.
Stages of Product Lifecycle
The Product Lifecycle is traditionally broken down into several stages, each crucial in its own right. From the earliest spark of an idea to the final sale and beyond, hereβs a closer look at these stages:
- Concept: This is where ideas are born. Companies explore market opportunities, gather customer feedback, and brainstorm innovative solutions. The goal here is to validate the idea before any resources are committed.
- Development: Once an idea is vetted, it enters the development phase. This includes everything from design to prototyping. Iterative testing often occurs here to refine the product. Itβs a vital stage where MRP can influence material sourcing and planning.
- Launch: As the product hits the market, companies must manage marketing, distribution, and inventory levels meticulously. Coordination between MRP and PLM becomes paramount to avoid stockouts or overproduction.
- Growth: Here, sales ramp up. Companies need to scale production and optimize supply chains. MRP systems help meet increased demand, ensuring that inventory levels align with sales forecasts.
- Maturity: At this point, sales stabilize. Organizations can leverage PLM data to understand trends and make informed decisions about potential improvements or adaptations needed.
- Decline: Inevitably, products may reach a decline. Effective PLM practices encompass planning for product discontinuation or transitioning to new offerings, ensuring minimal disruption.
"The awareness of where a product stands in its lifecycle can greatly influence timely business decisions."
Data Management and Compliance
In this digital age, managing data effectively is not just importantβitβs essential. PLM serves as a vault for all product-related data, encompassing everything from specifications to regulatory compliance documentation. Here are some key considerations:
- Centralized Data Repository: A unified platform for product data ensures all stakeholders have access to the most current information. This is particularly useful when marketing teams, engineers, and suppliers are not all in the same room but need aligned efforts.
- Regulatory Compliance: Different industries have varying regulations governing product data. PLM helps organizations keep track of compliance requirements, making it easier to manage audits or inspections.
- Version Control: Keeping track of different product versions is critical in ensuring that the right information is being used at each stage. With efficient data management, companies can mitigate risks associated with errors.
- Data Integration: Integrating PLM with other enterprise systems, such as MRP, is crucial. When data flows seamlessly between systems, organizations can gain insights that drive efficiency and support strategic decisions.
- Security and Access Control: Outlining clear protocols on who can access sensitive data helps protect intellectual property and maintain compliance.
By grasping these core principles of PLM, organizations position themselves to not only understand their products better but to also build a foundation for efficiency throughout the supply chain. Merging the knowledge of the product lifecycle with sound data management practices can yield a competitive edge that few can match.
The Interrelation Between MRP and PLM
Understanding the interplay between Material Requirements Planning (MRP) and Product Lifecycle Management (PLM) is not just a theoretical exercise; itβs a substantive exploration of how these two systems work synergistically in modern enterprises. The relation between them underpins operational efficiency, streamlined processes, and enhanced decision-making, making it a critical area of focus for business leaders, particularly those steering small to medium-sized businesses. As these organizations navigate the challenges of a competitive landscape, recognizing how MRP and PLM complement each other becomes essential.
When businesses effectively combine MRP with PLM, they unlock significant benefits and efficiencies. The alignment of production schedules with product designs allows for a more responsive supply chain. In addition, understanding their interdependencies helps to reduce costs, mitigate risks associated with product changes, and improve collaboration across different teams. Often, companies that neglect this relationship risk falling behind, as their operations could become fragmented, leading to inefficiencies that compromise product quality and timelines.
Shared Objectives
Both MRP and PLM serve essential functions within an organization, but itβs their shared objectives that truly strengthen their association. At the core, both aim to ensure that products are manufactured efficiently, meet market demands, and fulfill customer expectations. Whatβs particularly significant is realizing how both frameworks advocate for a holistic view of product evolution and resource allocation.
Key common goals include:
- Improving Time-to-Market: By coordinating product development timelines with material availability, companies can launch products on schedule, capturing market opportunities quickly.
- Enhancing Quality Control: Both systems emphasize the importance of maintaining high standards throughout the product lifecycle, leading to reduced defects and enhanced customer satisfaction.
- Optimizing Resource Utilization: In unison, MRP and PLM facilitate better forecasting and planning, ensuring that both human and material resources are used effectively.
These shared objectives make it clear that businesses that integrate MRP and PLM are better positioned to adapt to changes in consumer preferences and market conditions.
Data Synchronization Challenges
However, the road to seamless integration is wrought with challenges, particularly regarding data synchronization. In many organizations, MRP and PLM operate on separate platforms, resulting in silos that can lead to discrepancies in data. This separation can create a lack of visibility into product changes and inventory levels, ultimately hindering decision-making.
Businesses often grapple with:
- Inconsistent Data Formats: When different systems use varied formats for data entry, it becomes difficult to merge and analyze information effectively.
- Delayed Updates: Changes to product designs made in PLM may not immediately reflect in MRP systems, causing potential disruptions in planning and materials ordering.
- Resistance to Change: Employees accustomed to existing processes may resist adopting new integrated solutions, complicating implementation.
Addressing these challenges requires a commitment to fostering a culture of collaboration and support for technological solutions that enhance data coherence. Organizations must prioritize investing in compatible systems or middleware that facilitate effective communication between MRP and PLM tools.
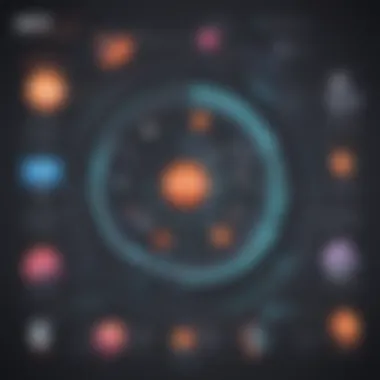
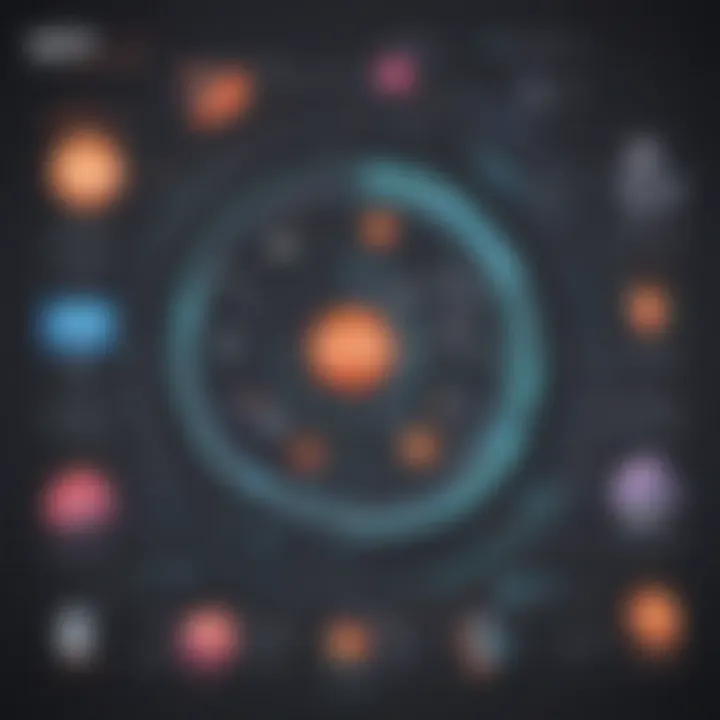
Impact on Business Processes
In todayβs fast-paced business world, the interplay between Material Requirements Planning (MRP) and Product Lifecycle Management (PLM) is vital. Understanding their impact on business processes is not just important; itβs crucial for companies aiming to enhance efficiency and leverage their resources better. Integrating these systems can lead to significant improvements that trickle down through various layers of an organization.
The seamless connection between MRP and PLM facilitates smoother operations. They help in digitizing and streamlining the entire product lifecycle, which encompasses the conceptual, development, and production stages. When these two systems function in harmony, they eliminate redundancies, allowing businesses to focus on what really mattersβcustomer satisfaction and product quality.
Operational Efficiency
Operational efficiency is at the heart of integrating MRP and PLM. This synergy allows for better resource management, as materials are tracked throughout their journeyβfrom procurement to the manufacturing floor. Companies can gain better visibility into their operations, which helps in identifying bottlenecks and inefficiencies. These insights often reveal hidden costs or resource allocations that could be optimized.
- Real-time Data: The unified system provides real-time data updates, empowering decision-makers to react swiftly to changes. For instance, if a supplier faces delays, organizations are immediately aware and can adjust their production plans accordingly.
- Better Planning: With harmonized data, businesses can better forecast demand patterns. By analyzing historical data within both systems, they can anticipate product needs with greater accuracy, leading to improved inventory management.
- Enhanced Collaboration: When MRP and PLM systems are integrated, different departments can work together seamlessly. For example, the engineering team can directly access inventory data, facilitating better communication and collaboration with the production team.
In this connected landscape, businesses often see lead times decrease, resulting in faster time-to-market for new products.
"A well-integrated MRP and PLM system can shrink lead times significantly, ensuring businesses stay ahead in the competitive marketplace."
Cost Reduction Strategies
Cost reduction strategies are another significant benefit derived from integrating MRP and PLM. By aligning these systems, organizations can uncover cost-saving opportunities at every phase of product development and production.
- Minimizing Waste: An effective MRP system ensures that the right amount of materials is ordered. When connected with PLM, it allows businesses to make informed decisions based on design changes or updates in product requirements, minimizing waste due to overordering or surplus materials.
- Reducing Inventory Costs: Enhanced data visibility leads to better inventory control. Companies can adopt a just-in-time manufacturing approach, which reduces holding costs and frees up capital for other operational needs.
- Streamlined Processes: Integrating the two systems allows for automating repetitive tasks. This not only saves labor costs but also reduces the potential for errors that can lead to costly delays or rework.
By focusing on these cost-reduction strategies, businesses not only improve their bottom lines but also enhance their overall competitiveness in the market.
Challenges in Integrating MRP and PLM
The marriage of Material Requirements Planning (MRP) and Product Lifecycle Management (PLM) systems is often viewed as a strategic advantage for modern enterprises. Yet, the journey of integration is not smooth sailing. In fact, several challenges arise that can hinder this collaboration, impacting overall productivity and efficiency. Grasping these challenges is essential not only for IT managers and decision-makers but also for small to medium-sized businesses that aim to leverage these systems effectively. This section explores the key elements that pose challenges, emphasizing how to navigate them for a successful integration.
Technological Barriers
One of the prominent hurdles in integrating MRP and PLM lies in technological compatibility. MRP systems are often built to manage inventory and production schedules, whereas PLM tends to focus more on the lifecycle of product development. When these two systems are not designed to work together, data silos can form, leading to inconsistencies that could boggle down decision-making.
Consider, for instance, an organization relying on outdated MRP software that lacks modern APIs for data exchange. Such limitations make it tricky to align data from the PLM system that manages product specifications, changes, and advanced analytics. This disconnect can lead to several operational issues, such as misunderstanding customer demands, excess inventory, or even missed market opportunities.
To address these technological barriers, businesses must invest in solutions that facilitate an easier data flow. Cloud-based systems often provide the much-needed flexibility and framework for seamless integration. But it's not just about adopting new technologies. Upgrading the skills of the workforce is another essential step. Training sessions should focus on how different teams can use both systems efficiently, making sure everyone is on the same page.
Cultural Resistance within Organizations
The second challenge arises from the internal culture of an organization. A significant number of employees may feel resistant to change, especially when it involves altering established workflows or learning new systems. This resistance can manifest in various ways: some may hesistate to embrace collaborative tools that allow for greater transparency between departments.
To illustrate, an engineering team might think that MRP overlooks product development considerations, while the production team could feel that PLM complicates the supply chain. When these sentiments go unaddressed, silos become entrenched, and the integration suffers. This cultural tension can act as a damper on enhancing efficiency, leading to misunderstandings that can inhibit innovation.
Fostering a culture of collaboration can be the antidote to this challenge. Open forums where individuals from different departments can share their insights and concerns can serve to ease fears and clarify misconceptions. Communication plays a pivotal role in this. Establishing clear objectives for both systems and defining how they complement each other can help dispel doubts and build trust among teams.
"Integration does not merely imply combining systems; it requires a tenacious commitment to bridging gaps in culture and technology."
In the end, understanding these challenges and tackling them head-on is essential for integrating MRP and PLM effectively. By addressing both technological barriers and cultural resistance, small to medium-sized businesses can pave the way for enhanced operational efficiency, ultimately leading to a more cohesive approach to product lifecycle management and material requirements planning.
Best Practices for Combining MRP and PLM
Combining Material Requirements Planning (MRP) and Product Lifecycle Management (PLM) is not just a matter of convenience; it can fundamentally reshape how businesses operate, particularly for small to medium-sized enterprises. The seamless integration of these two systems leads to improved efficiency, better data management, and more informed decision-making. This section will discuss best practices that organizations should consider when merging MRP and PLM.
Creating a Unified Strategy
To get the best out of MRP and PLM, businesses need to start with a unified strategy that aligns both systems with the organizationβs overall objectives. Each department, from production to marketing, has its own KPIs. When they work separately, those KPIs often donβt support each other, leading to confusion and inefficiencies.
- Align Goals: Begin by ensuring that the goals of both MRP and PLM are aligned with business objectives. For example, if your aim is to reduce production costs, both teams need to collaborate on how inventory decisions (MRP) can support product design choices (PLM).
- Establish Clear Roles: Define the roles of each stakeholder in both systems. Who is responsible for data entry? Who reviews the accuracy of the data? By eliminating ambiguity in roles, companies can streamline processes and reduce errors.
- Implement Centralized Data Management: Itβs essential that MRP and PLM systems share a common database or interface. With a centralized approach, you can ensure that data such as inventory levels and product specifications are consistent across departments.
- Feedback Loops: Create mechanisms for ongoing feedback between MRP and PLM users. Regularly scheduled meetings to discuss issues, discrepancies, and results can foster a better understanding of how each side operates, thus leading to a more cohesive strategy overall.
These practices help not only streamline operations but also enrich the decision-making processes across the board, resulting in a more agile organization.
Fostering Cross-Department Collaboration
Another cornerstone of merging MRP and PLM successfully is fostering effective collaboration between departments. In many organizations, the silos between departments can impede data flow and lead to complications down the line.
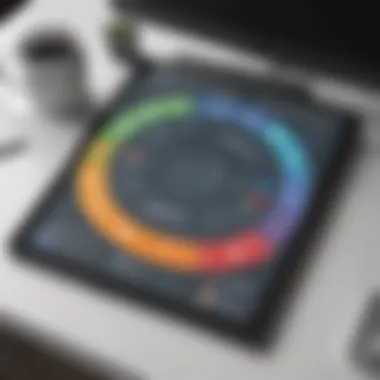
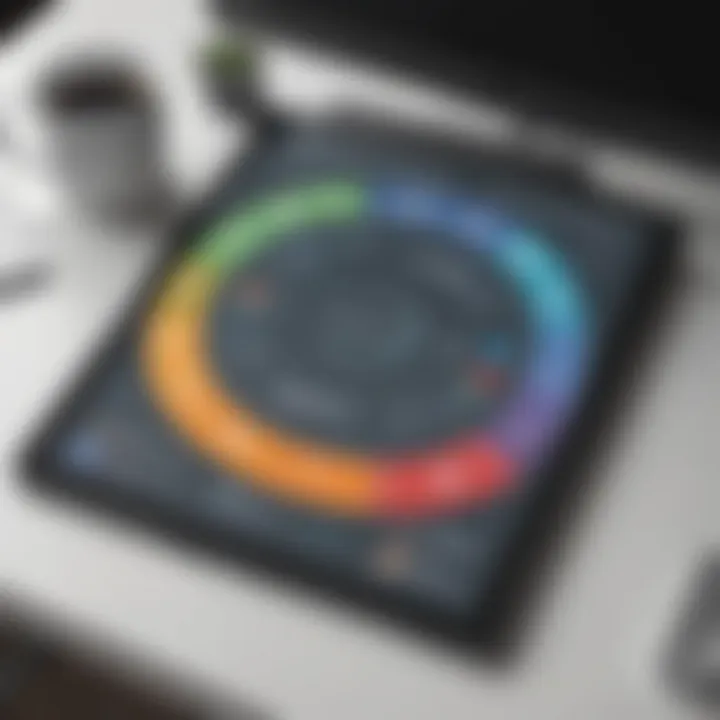
- Build Interdisciplinary Teams: Form task forces composed of members from the production, engineering, and marketing departments. When people from different backgrounds collaborate, they can identify potential areas of conflict and take corrective action before problems escalate.
- Promote Transparency: Encourage open forums where employees can share insights and challenges they encounter while using MRP and PLM. When everyone understands what is at stake and how each system impacts others, it leads to better cooperation.
- Use Collaboration Tools: Invest in software that enables real-time communication between departments. Tools like Slack or Trello can facilitate discussions about both product lifecycles and material requirements in an accessible way.
- Training & Workshops: Periodically schedule workshops to educate team members about how MRP and PLM function and interact. This can help demystify processes and encourage people to take ownership of their roles within the integrated framework.
Through these collaborative efforts, businesses can create an environment where MRP and PLM not only coexist but thrive together.
"Integration isnβt just about technology. Itβs about people; their processes, their culture, and their willingness to adapt."
Using these best practices, organizations can pave the way for a more fluid and effective integration of MRP and PLM that ultimately benefits the entire operation.
Case Studies of Successful MRP and PLM Integration
When discussing the application of both MRP and PLM, there's no better approach than to scrutinize real-world examples. The integration of Material Requirements Planning (MRP) and Product Lifecycle Management (PLM) isn't just theoretical speculation; it's a practical concern that many businesses grapple with every day. In this section, we will spotlight how various businesses have successfully harmonized these systems, and what benefits have followed suit.
The importance of exploring case studies in this context cannot be overstated. Businesses are often parched for insights that show tangible proof of concept. Understanding the intricacies of these integrations can help organizations tailor their approaches to achieve measurable improvements. Not every industry or company will benefit in the same way, so examining detailed examples offers warm insights into the methods and results that can be expected.
Industry Leaders' Insights
Some industry leaders have paved the way for effectively merging MRP and PLM, leading to impressive outcomes. Take Caterpillar, for instance. Their approach blended the MRP framework with PLM systems, creating a synergy that improved inventory management and streamlined their product development. This integration enabled them to reduce lead times significantly and to ensure that the right materials were always available at the right time.
Moreover, Boeing has used this integration to bolster its supply chain performance. By having real-time data flowing between MRP and PLM, they enhanced communication across departments, leading to faster decision-making. This efficient flow of data means fewer delays and less waste, which are objectives every modern enterprise strives for. Their insights emphasize a clear takeaway: when implemented thoughtfully, this integration fosters responsive manufacturing processes that can adapt swiftly to market demands.
Lessons Learned from Failures
However, it's crucial to analyze not just the success stories but the cautionary tales as well. Missed opportunities exist for businesses that dive headfirst into these integrations without due diligence. The case of General Motors serves as a wake-up call. In the past, they faced hurdles when trying to sync their MRP and PLM systems, resulting in high operational costs and longer times to market. The lesson here is that technology alone doesn't guarantee success. A disjointed implementation, especially one that lacks user training or clear communication across teams, can result in chaos rather than harmony.
Another instance involves a prominent electronics manufacturer that encountered significant pitfalls when integrating MRP and PLM systems. The lack of consistent data standards and poor alignment between departments led to mismatched inventory and unnecessary delays in product launches. Their takeaway? Build comprehensive training and ongoing support into your integration plan; itβs not just about the tech β it's about the people who utilize it.
Successful integration of MRP and PLM is a marathon, not a sprint. Organizations must remain vigilant and patient as they adapt these systems to their needs.
Future Trends in MRP and PLM
The landscape of Material Requirements Planning (MRP) and Product Lifecycle Management (PLM) is undergoing transformative changes. As modern enterprises become more complex, understanding the future trends in these systems is crucial. This section delves into how emerging technologies and shifting industry benchmarks are reshaping MRP and PLM, particularly for small to medium-sized businesses, entrepreneurs, and IT professionals.
Emerging Technologies Impacting MRP
In today's fast-paced environment, technology serves as a backbone for almost every business function. MRP systems are not excluded from this trend. Some key technologies reshaping MRP include:
- Artificial Intelligence: Machine learning algorithms enable predictive analytics, allowing businesses to better forecast demand and inventory needs. This adaptability can notably reduce costs associated with surplus or insufficient inventory.
- Cloud Computing: The flexibility and scalability offered by cloud-based MRP solutions are game-changers. Companies can easily access data from anywhere, promoting collaboration and improving decision-making.
- Internet of Things (IoT): Real-time data collection from connected devices enhances inventory management. For example, a smart shelf can notify inventory managers when stock levels hit a specific threshold, leading to more timely replenishments.
These technologies encourage a more agile approach to MRP, allowing companies to react swiftly to market fluctuations. This increased responsiveness can directly impact customer satisfaction and ultimately revenue.
Trends Shaping PLM Practices
As product strategies evolve, PLM practices are also seeing significant shifts. Notable trends shaping PLM include:
- Sustainability Focus: Corporations are increasingly aware of their environmental impact. Practices like eco-design are on the rise, ensuring that products are energy efficient and recyclable, aligning with consumer expectations for greener products.
- Collaborative Platforms: The move towards teamwork is evident. Tools that promote cross-department communication facilitate quicker resolutions and enhance product development timelines. A unified workspace can make all the difference in keeping everyone on the same page.
- Data-Driven Insights: Companies are adopting analytics to glean insights from their product data in the PLM stage. Businesses that effectively harness this data are more likely to innovate and bring successful products to market faster.
Shaping PLM practices along these lines means organizations can stay ahead of the competition, ensuring they remain relevant in a rapidly changing market.
"The future belongs to those who prepare for it today."
β Malcolm X
By embracing these trends, businesses can position themselves not just to survive, but to thrive in the arena of MRP and PLM. As they integrate these revelations into their practices, they're likely to see enhanced efficiency, improved collaboration, and more informed decision-making.
Finale
The relationship between Material Requirements Planning (MRP) and Product Lifecycle Management (PLM) within modern enterprises has proven to be fundamental for thriving in today's competitive landscape. This analysis shines a spotlight on how effective integration can lead to substantial operational gains.
Summarizing Key Takeaways
In the intricate dance of MRP and PLM, several key points emerge:
- Efficiency and Accuracy: A cohesive approach minimizes errors and maximizes accuracy in inventory management. If one system knows what the other is doing, the risk of miscommunication diminishes.
- Improved Decision Making: With aligned objectives and synchronized data, organizations can make better-informed decisions that reflect real-time market demands.
- Cost Management: Effective collaboration helps bypass excessive overhead costs associated with misalignment. Saving here doesnβt just keep the company afloat, it keeps it competitive.
- Agility in Response: In a world where change is the only constant, businesses utilizing both MRP and PLM can adjust their strategies on-the-fly, addressing market needs as they arise.
"Integration is not just about software; itβs a strategic alignment that paves the way for transformative business practices."
Looking Toward Future Implementations
As we gaze into the horizon, itβs clear that the interplay between MRP and PLM will continue to evolve. Companies must consider the following aspects when planning future implementations:
- Adoption of Emerging Tech: The incorporation of AI and machine learning within MRP and PLM systems will provide unprecedented predictive capabilities, enhancing decision-making.
- Scalability and Flexibility: Future solutions should accommodate growth and changes in business strategies without compromising performance.
- Sustainability Focus: With environmental concerns on the rise, integrating sustainability frameworks within both systems will not only enhance compliance but also resonate with contemporary consumer values.
- Enhanced Communication Channels: Emphasizing transparent communication throughout departments will support a more synchronized approach, breaking down silos that currently exist.
Investing in these areas will not only optimize current processes but also prepare organizations to tackle the inevitable challenges and opportunities ahead, securing their positions in a rapidly changing marketplace.